I have a little over 45oo miles on mine from last year. It did not work well. serviced my sled last month and the bearing was flopping around. Shaft was worn down to 1.65 inches. I did not have the wedge in all the way, had it to where you could get a wrench on the flat spots. Had it torqued to 35ft/lbs. Got a brand new shaft, put the wedge all the way in to the washer and set torque to 45ft/lbs for this year. As bad as mine was worn, I had no symptoms on the sled. Place I sent it to be fixed said I had the worst one he has seen.

hibshman25
Vendor
- Joined
- Sep 25, 2005
- Messages
- 2,856
- Age
- 40
- Location
- Lebanon, PA 17042
- Country
- USA
- Snowmobile
- 2017 sidewinder ltx dx
2018 snoscoot
I have had one customer reach out to me to inform me that his shaft still spun. If I recall he had set it to 30-35 ft lbs while on the machine. If you can't do an actual bench test with the lock on drive shaft to determine a torque I have now been suggesting going more than the 30-35 to ensure it is locked down. Tolerance inconsistency on these shafts is the whole reason we are even in this thread, so 30-35 ft lbs is not going to work on all shafts. Some will need more expansion than others. My feelings are if a shaft still spins it simply just wasn't tight enough.
On another note, I've had some some threaded wedge samples made from a harder material. I intend to do some extreme testing with these to see if I can get the wedge to work on slightly worn shafts. The current production version the threads strip when pushed to limit on a worn shaft.
On another note, I've had some some threaded wedge samples made from a harder material. I intend to do some extreme testing with these to see if I can get the wedge to work on slightly worn shafts. The current production version the threads strip when pushed to limit on a worn shaft.

hibshman25
Vendor
- Joined
- Sep 25, 2005
- Messages
- 2,856
- Age
- 40
- Location
- Lebanon, PA 17042
- Country
- USA
- Snowmobile
- 2017 sidewinder ltx dx
2018 snoscoot
I have a little over 45oo miles on mine from last year. It did not work well. serviced my sled last month and the bearing was flopping around. Shaft was worn down to 1.65 inches. I did not have the wedge in all the way, had it to where you could get a wrench on the flat spots. Had it torqued to 35ft/lbs. Got a brand new shaft, put the wedge all the way in to the washer and set torque to 45ft/lbs for this year. As bad as mine was worn, I had no symptoms on the sled. Place I sent it to be fixed said I had the worst one he has seen.
Ironic we were both typing up posts at the same time and you were the customer I was referring to. I assume you bench tested prior to assembly. Did it get tight at 30-35 and you just went extra?
So I wanted to update my BOP Wedge usage. As you can see from the pics the shaft was warn pretty good, but with the additional torque there was no evidence of the shaft spinning in the bearing race after last seasons use.2017 LTX LE call it 3800 miles, i had it apart last season and it was fine, no wear at all. Took it apart last weekend and It now showed it had spun, but not bad enough to replace. Cleaned it up inside and out and at 55 lbs made it firm so i gave it an extra bump to 60 ft lbs. Used never seize on the contact surfaces and blue locktite on the bolt. View attachment 151475
I had the shaft replaced under warranty before it expires and the Nachi bearing looked new so it was put back on the new shaft. I will remove the bearing to repack and test how much torque is needed to once again lock the bearing to the shaft with the BOP Wedge. Moral of the story, don't be afraid to torque these things up if they need it.
Crossfire12
TY 4 Stroke Guru
- Joined
- Feb 13, 2017
- Messages
- 883
- Age
- 68
- Location
- New York Adirondacks
- Country
- USA
- Snowmobile
- 2010 Z1 Turbo ,2017 zr9000, F1100 turbo, 700 srx
- LOCATION
- Sacandaga reservoir
It doesn’t work.....back to the drawing board
WinderFab
TY 4 Stroke God
- Joined
- Mar 1, 2009
- Messages
- 1,862
- Age
- 46
- Location
- Woodbridge, ON
- Country
- Canada
- Snowmobile
- 2020 Sidewinder Ltx GT
Just over 3500 km and mine has worked great so far..
Like hibshman25 you need to bench test it to see what torque is needed, I removed my roto and calliper reinstalled the bearing on the shaft and torqued the wedge till the bearing was tight on shaft, mine at 35lbs was tight so I went to 40lbs when I reinstalled everything back on the sled.
A little extra work goes along ways, if done right the wedge works..
Like hibshman25 you need to bench test it to see what torque is needed, I removed my roto and calliper reinstalled the bearing on the shaft and torqued the wedge till the bearing was tight on shaft, mine at 35lbs was tight so I went to 40lbs when I reinstalled everything back on the sled.
A little extra work goes along ways, if done right the wedge works..
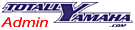

- Joined
- Apr 13, 2003
- Messages
- 21,350
- Age
- 54
- Location
- Schofield, WI
- Website
- www.totallyamaha.com
- Country
- USA
- Snowmobile
- 2020 Sidewinder SRX
Just over 3500 km and mine has worked great so far..
Like hibshman25 you need to bench test it to see what torque is needed, I removed my roto and calliper reinstalled the bearing on the shaft and torqued the wedge till the bearing was tight on shaft, mine at 35lbs was tight so I went to 40lbs when I reinstalled everything back on the sled.
A little extra work goes along ways, if done right the wedge works..
I can agree but I bench tested one like that and it still spun... not all will hold for some reason. I cant say it dont work because some have and some have not that I have done and dont understand why. The last few I have done in my shop was spray metal to size and size and a FAG bearing and they have not come back with a bad shaft so far but time will tell.
yamamarc
TY 4 Stroke God
- Joined
- Sep 29, 2013
- Messages
- 3,051
- Location
- Massey Ontario
- Country
- Canada
- Snowmobile
- 2019 zr9000 Ltd
I can agree but I bench tested one like that and it still spun... not all will hold for some reason. I cant say it dont work because some have and some have not that I have done and dont understand why. The last few I have done in my shop was spray metal to size and size and a FAG bearing and they have not come back with a bad shaft so far but time will tell.
I been having great luck with drilling 4 divets and using retaining compound on multiple 998's
I needed a puller and lots of heat to get the bearing to release off the shaft
I have a spare shaft on hand that I need to get spray welded and machined And out on shelf as spare incase someone needs one during the season.
Did you make your a"shoulder fit " or did you over size the shaft a bit ?
This is the left over retaining compound once I got the bearing off
Shaft cleaned up
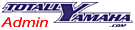

- Joined
- Apr 13, 2003
- Messages
- 21,350
- Age
- 54
- Location
- Schofield, WI
- Website
- www.totallyamaha.com
- Country
- USA
- Snowmobile
- 2020 Sidewinder SRX
I been having great luck with drilling 4 divets and using retaining compound on multiple 998's
I needed a puller and lots of heat to get the bearing to release off the shaft
I have a spare shaft on hand that I need to get spray welded and machined And out on shelf as spare incase someone needs one during the season.
Did you make your a"shoulder fit " or did you over size the shaft a bit ?
This is the left over retaining compound once I got the bearing off
View attachment 156852
Shaft cleaned up
View attachment 156851
Machined down the warn shaft and then built it up to be size on size to the inner race of bearing.
Don't want to sound like a broken record, but ......IF somebody would come up with a shaft that would be "closer" to an interference fit....something we can cool the shaft with a can of duster spray(HFC) and heat the bearing in the oven so it would slide on, they would be in high demand. I know I would buy one!
ClutchMaster
HUGE Member
- Joined
- Jan 18, 2016
- Messages
- 2,996
- Location
- tomahawk
- Country
- USA
- Snowmobile
- 2015 Viper 270 hurricane,
2002 Viper W/162 A.C. skid, SRX pipes &CDI, 780 BB
- LOCATION
- Wisconsin
It doesn’t work.....back to the drawing board
You just have to be smart enough to install it correctly, so I see your problem.
I have had one customer reach out to me to inform me that his shaft still spun. If I recall he had set it to 30-35 ft lbs while on the machine. If you can't do an actual bench test with the lock on drive shaft to determine a torque I have now been suggesting going more than the 30-35 to ensure it is locked down. Tolerance inconsistency on these shafts is the whole reason we are even in this thread, so 30-35 ft lbs is not going to work on all shafts. Some will need more expansion than others. My feelings are if a shaft still spins it simply just wasn't tight enough.
On another note, I've had some some threaded wedge samples made from a harder material. I intend to do some extreme testing with these to see if I can get the wedge to work on slightly worn shafts. The current production version the threads strip when pushed to limit on a worn shaft.
Agreed the shaft can’t be worn or have excessive clearance. It will expand the shaft no more than .0035” of an inch @ 55 ft/lbs of torque, so it won’t fix worn shafts.
On the bench I’ve found it won’t even expand the shaft .0015” if it’s not properly greased on the ramps and threads and inserted as far in as possible.
The nice thing is for removal of your driveshaft you need no pullers to get the shaft out. Just loosen the McWeggie and the driveshaft will come right out. No issues I just had mine apart.
gsxr
TY 4 Stroke Master
- Joined
- Feb 24, 2006
- Messages
- 1,338
- Location
- BRACEBRIDGE , ONTARIO
- Country
- Canada
- Snowmobile
- 2023 SRX
We tightened till the rotor snugged up then backed off till it floated again. 55 ft lbs. all good on 5 sleds.
I would go to the max torque of the bolt supplied which is 460-515 inch/lbs. I set mine to 45 ft/lbs. It got tight at 35, went to 45.Ironic we were both typing up posts at the same time and you were the customer I was referring to. I assume you bench tested prior to assembly. Did it get tight at 30-35 and you just went extra?
Take into consideration those are suggested torque values and not max torque values. Mine was torqued to 60 ft lbs and it prevented slippage. It also helps greatly to load all contact surfaces on the McWedggie with grease or never seize to get an accurate torque value. Seems every bearing fit differs from the next so i just wanted guys to know that i wouldn't stop at 45 ft lbs unless it was good and snug at 40 ft lbs. Remember, there will be temp changes when that bearing starts to heat up ripping across the lake at 120 MPH!I would go to the max torque of the bolt supplied which is 460-515 inch/lbs. I set mine to 45 ft/lbs. It got tight at 35, went to 45.
Last edited:
sab2022
Expert
I've scanned the 43 pages herein, and watched the BOP wedge video (twice) being installed on shaft(s) located on work bench(s). As Newbie everyone is telling me how to do steps 5 - 10, but what I really want to know is how to do steps 1 - 5?
Am I removing the caliper? Black screws? Rotor? One piece (assembly). Loosening screws? Remove the a snap ring
OR, do just put the &$%# "thing" in there with some light grease like Travis says, torque it to 33 lbs and say see you next summer when I inspect the bearing.
OR, should I do nothing at all (i.e. brand new 2020 Covid touring sled never seen snow), BUT that action would be in violation of about 15 TY posts. that say......"the 1st thing you do when new is install BOP driveshaft saver before... etc, etc".
I'm leaning to putting the &$%# "thing" in there and torquing it. I shouldn't have to remove the skid to install this BOP part
Thanks. (Note below there's a Precision EFI belly pan in the way, I like those.)
Am I removing the caliper? Black screws? Rotor? One piece (assembly). Loosening screws? Remove the a snap ring
OR, do just put the &$%# "thing" in there with some light grease like Travis says, torque it to 33 lbs and say see you next summer when I inspect the bearing.
OR, should I do nothing at all (i.e. brand new 2020 Covid touring sled never seen snow), BUT that action would be in violation of about 15 TY posts. that say......"the 1st thing you do when new is install BOP driveshaft saver before... etc, etc".
I'm leaning to putting the &$%# "thing" in there and torquing it. I shouldn't have to remove the skid to install this BOP part
Thanks. (Note below there's a Precision EFI belly pan in the way, I like those.)
Similar threads
- Replies
- 6
- Views
- 2K
- Replies
- 36
- Views
- 6K
- Replies
- 327
- Views
- 52K
- Replies
- 21
- Views
- 33K
-
This site uses cookies to help personalise content, tailor your experience and to keep you logged in if you register.
By continuing to use this site, you are consenting to our use of cookies.