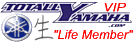

- Joined
- Jun 1, 2004
- Messages
- 7,695
- Location
- sudbury on
- Country
- Canada
- Snowmobile
- 2016 apex xtx
2011 apex xtx
2009 phaser rtx/x
1997 et410t/r
1988 vk 540
you could always cut the box end off of a cheap wrench and then weld a socket to it.
i usually just lean into it with the crecent to tighten it. i have removed one with a chisel as it was not coming loose with any type wrench.
i usually just lean into it with the crecent to tighten it. i have removed one with a chisel as it was not coming loose with any type wrench.

RobX-1
VIP Member
- Joined
- Apr 13, 2003
- Messages
- 2,084
- Location
- Coldwater, OH
- Country
- USA
- Snowmobile
- 18 50th Apex XT-X, 08 40th Apex LTX GT, 08 40th Nytro RTX, & 03 RX-1
Here's a link to the one I purchased from JB Tool although it shows it being out of stock; shocker like anything else.
https://www.jbtools.com/grey-pneumatic-2036xmd-1-2-drive-x-36mm-extra-deep-socket/
And like main suggested, here's a link to a post I had created about said socket and Red Beard showing you what main is referring to
https://ty4stroke.com/threads/yamaha-chain-case-top-gear-36mm-socket.150272/#post-1391984
https://www.jbtools.com/grey-pneumatic-2036xmd-1-2-drive-x-36mm-extra-deep-socket/
And like main suggested, here's a link to a post I had created about said socket and Red Beard showing you what main is referring to
https://ty4stroke.com/threads/yamaha-chain-case-top-gear-36mm-socket.150272/#post-1391984
ApexGT06Canuck
Newbie
- Joined
- Jan 25, 2022
- Messages
- 19
- Location
- Whitby, Ontario
- Country
- Canada
- Snowmobile
- 2006 Yamaha Apex GT
I had seen your post Rob and that's the socket I found on Amazon for $177, also out of stock.
I don't have access to welding equipment so I would have to take a cut socket to get fab'd. I might just use an adjustable however I would feel more comfortable being able to torque it.
I don't have access to welding equipment so I would have to take a cut socket to get fab'd. I might just use an adjustable however I would feel more comfortable being able to torque it.

RobX-1
VIP Member
- Joined
- Apr 13, 2003
- Messages
- 2,084
- Location
- Coldwater, OH
- Country
- USA
- Snowmobile
- 18 50th Apex XT-X, 08 40th Apex LTX GT, 08 40th Nytro RTX, & 03 RX-1
In all honesty, a large adjustable crescent wrench is what I had used prior to obtaining the deep well 36mm socket but like you, also wanted to torque that nut to spec; if for anything else, just the peace of mind.
ApexGT06Canuck
Newbie
- Joined
- Jan 25, 2022
- Messages
- 19
- Location
- Whitby, Ontario
- Country
- Canada
- Snowmobile
- 2006 Yamaha Apex GT
For the rivets, which 3/16" rivets which part number would i be looking at?
I assume I'd want to go with the larger grip radius?
I assume I'd want to go with the larger grip radius?

RobX-1
VIP Member
- Joined
- Apr 13, 2003
- Messages
- 2,084
- Location
- Coldwater, OH
- Country
- USA
- Snowmobile
- 18 50th Apex XT-X, 08 40th Apex LTX GT, 08 40th Nytro RTX, & 03 RX-1
Yes, the ones I used were the second link; the 0.059 - 0.354 Inch Grip

RobX-1
VIP Member
- Joined
- Apr 13, 2003
- Messages
- 2,084
- Location
- Coldwater, OH
- Country
- USA
- Snowmobile
- 18 50th Apex XT-X, 08 40th Apex LTX GT, 08 40th Nytro RTX, & 03 RX-1
That's also in line with what I paid for a bag of 100 on eBay; with shipping factored in, it was approx. $20
ApexGT06Canuck
Newbie
- Joined
- Jan 25, 2022
- Messages
- 19
- Location
- Whitby, Ontario
- Country
- Canada
- Snowmobile
- 2006 Yamaha Apex GT
Awesome thanks! No local suppliers had them in stock so I bought just enough from the stealership to get on the trail. I'm going to grab a box of the advel's for future service!
My shock rebuild is ready early! Now a mad scramble to finish everything to get out tomorrow!
I need the torque specs for all of the work I listed in the previous post, should I PM Mr.sled to get my status updated so that I can receive the service manual? I can post my receipt for VIP payment if needed.
I mainly need the crankcase, driveshaft bearing, speedo sensor, skid & carbide info.
My shock rebuild is ready early! Now a mad scramble to finish everything to get out tomorrow!
I need the torque specs for all of the work I listed in the previous post, should I PM Mr.sled to get my status updated so that I can receive the service manual? I can post my receipt for VIP payment if needed.
I mainly need the crankcase, driveshaft bearing, speedo sensor, skid & carbide info.
ApexGT06Canuck
Newbie
- Joined
- Jan 25, 2022
- Messages
- 19
- Location
- Whitby, Ontario
- Country
- Canada
- Snowmobile
- 2006 Yamaha Apex GT
Also to those interested. I found the tool from the crankcase gear removal how to. It's actually a tool to remove old Volkswagen rear axle nuts.
EMPI 5748, found it on Amazon.com for ~$50 CAD shipped. I'm using a crescent wrench for now but will be grabbing this for future service.
EMPI 5748, found it on Amazon.com for ~$50 CAD shipped. I'm using a crescent wrench for now but will be grabbing this for future service.
Amazon.com: Empi 5748 Vw Axle Nut Tool 36mm, Classic Volkswagen Bug Ghia Type 3 : Automotive
Buy Empi 5748 Vw Axle Nut Tool 36mm, Classic Volkswagen Bug Ghia Type 3: Axle Tools - Amazon.com ✓ FREE DELIVERY possible on eligible purchases
www.amazon.com
ApexGT06Canuck
Newbie
- Joined
- Jan 25, 2022
- Messages
- 19
- Location
- Whitby, Ontario
- Country
- Canada
- Snowmobile
- 2006 Yamaha Apex GT
So im working on studding the new track; Stud Boy Power Point 1.375" with power plate backers. Is there a torque spec with these? Their website states, "Tighten the stud assembly using a deep well socket and allen wrench until the stud and backer plate bottom out against each other." .
This leaves it up to interpretation IMO, how do you tell when the stud shoulder has contacted the backer plate? Woody's instructions state 15 ft/lbs. I was considering following this instead. I've read lots of threads recommending blue or red loctite on studs, however stud boy recommends no loctite with nylon locking nuts, any recommendations here?
This leaves it up to interpretation IMO, how do you tell when the stud shoulder has contacted the backer plate? Woody's instructions state 15 ft/lbs. I was considering following this instead. I've read lots of threads recommending blue or red loctite on studs, however stud boy recommends no loctite with nylon locking nuts, any recommendations here?
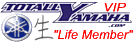

sxr70001
Lifetime Member
- Joined
- Dec 4, 2010
- Messages
- 1,110
- Location
- Michigan
- Country
- USA
- Snowmobile
- Sidewinder LTX SE
SR Viper RTX SE
You can also use a fishing scale or something on the end of a wrench to approximate a torgue wrench. 1 pound of force at the end of a 12 inch wrench=1 foot pound. Personally I just tighten the nut up and don't worry about it. To each his own. You will find that many of the members on this forum are perfectionists.
ApexGT06Canuck
Newbie
- Joined
- Jan 25, 2022
- Messages
- 19
- Location
- Whitby, Ontario
- Country
- Canada
- Snowmobile
- 2006 Yamaha Apex GT
I've got the crankcase back together and new track in, driveshaft bearing replaced, exhaust together, y pipe bracket and stud protectors riveted back in. Got the 36mm nut mantight, should be good to go
Still have to service the skid, carbides, swap in headlight assembly, Coolant swap and some other small stuff.
Thanks for all the help everyone
Still have to service the skid, carbides, swap in headlight assembly, Coolant swap and some other small stuff.
Thanks for all the help everyone
ApexGT06Canuck
Newbie
- Joined
- Jan 25, 2022
- Messages
- 19
- Location
- Whitby, Ontario
- Country
- Canada
- Snowmobile
- 2006 Yamaha Apex GT
Similar threads
- Replies
- 1
- Views
- 290
- Replies
- 7
- Views
- 3K
-
This site uses cookies to help personalise content, tailor your experience and to keep you logged in if you register.
By continuing to use this site, you are consenting to our use of cookies.